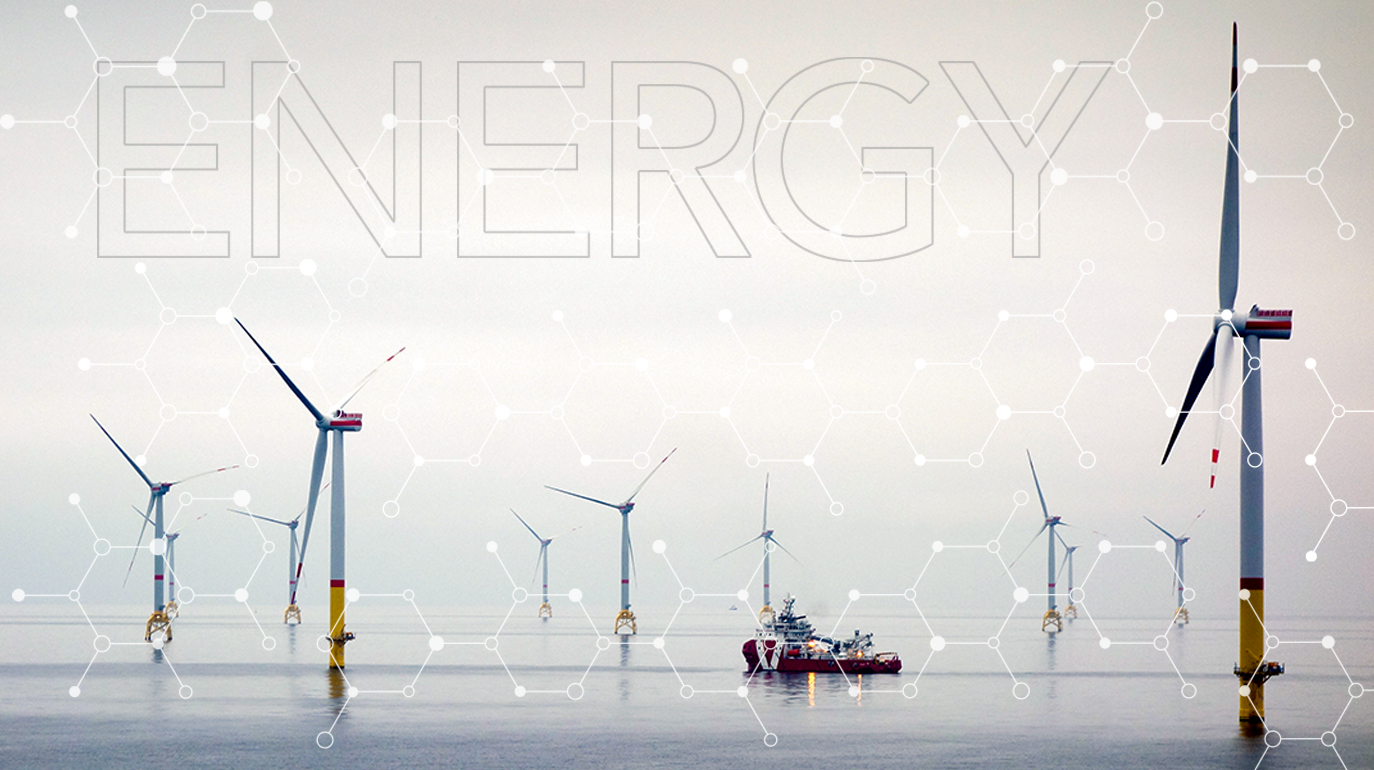
Cost-Effective Structural Health Monitoring for Offshore Wind Monopiles
Monopiles are the predominant foundation type in the offshore wind industry. As the sole load path from the turbine to the seabed, the structural integrity of the monopile is of significant importance to offshore wind farm operation. For monopile foundations, the region below the seabed is critical since this region sees the largest bending loads and operators may elect to instrument and monitor monopiles in this region to support integrity management. Below seabed monitoring systems are extremely challenging to install and come at a high cost.
Background
The offshore wind industry is experiencing significant global growth, with substantial capacity additions in Europe, Asia, and the emerging U.S. market, which alone has over 52 GW of projects in development. As turbine sizes increase, with 15 MW units expected to become standard, the industry faces escalating costs in redesigning turbines, foundations, and installation vessels. To manage these costs and maintenance expenses, operators are turning to advanced monitoring and digital solutions, including digital twins, to reduce sensor needs and avoid outfitting every turbine with instruments. This approach aims to lower capital expenditures and support maintenance cost reduction through risk-based inspection and condition-based maintenance strategies. However, there is still a significant need for monitoring systems, particularly for foundations. Monopiles are the predominant foundation type in the offshore wind industry and must continuously withstand significant seabed bending loads without being inspected routinely for damage. Sub-seabed health monitoring systems allow for assessment of monopile integrity during their life. These monitoring systems contain sensitive instruments and cabling that can become damaged during installation and throughout the life of the monopile if left unprotected.
The Challenge
The health monitoring system sensors are susceptible to damage during installation process, namely the violent loading during pile driving, and the monitoring system needs to withstand this operation. Additionally, each foundation is a site-specific design and developers typically have varying requirements for monitoring. As a result, there are no standardized solutions which results in challenges in implementing cost-effective measurement systems. This drives the need for low-cost, robust designs for sub-seabed sensors and protection systems for those sensors and associated cables that are easy to install and can withstand the rigors of pile driving monopiles. Such a protection system would aid in reducing the high cost and complexity of implementing monitoring solutions, which are crucial for the longevity and efficiency of wind farms.
The Solution
SES Renewables Solutions developed two innovative, cost-effective monitoring protection solutions that could be easily implemented onto a monopile foundation and withstand the harsh conditions typical of pile driving installation operation. These two designs are named the “bolted” and “bonded” designs and are shown in Figures 1 and 2. These designs utilize off-the-shelf components and were validated by SES through sub-scale testing and finite element analysis. The bolted design is the simpler of the two that were tested, consisting of only an inverted steel C-channel bolted to steel mounting brackets that are welded to the monopile. The bonded design consists of two steel C-channels and a top plate. As with the bolted design, the C-channel is bolted to mounting brackets, but adhesive is also applied at this interface.
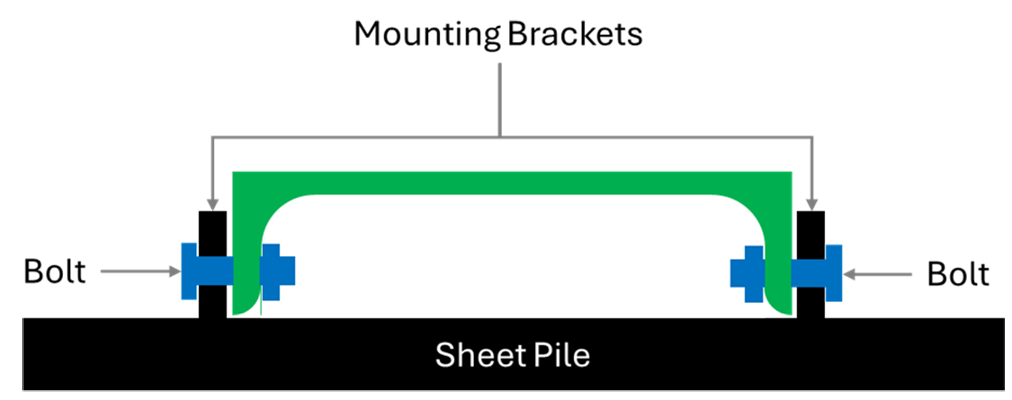
Figure 1. Bolted Sensor Protection Design
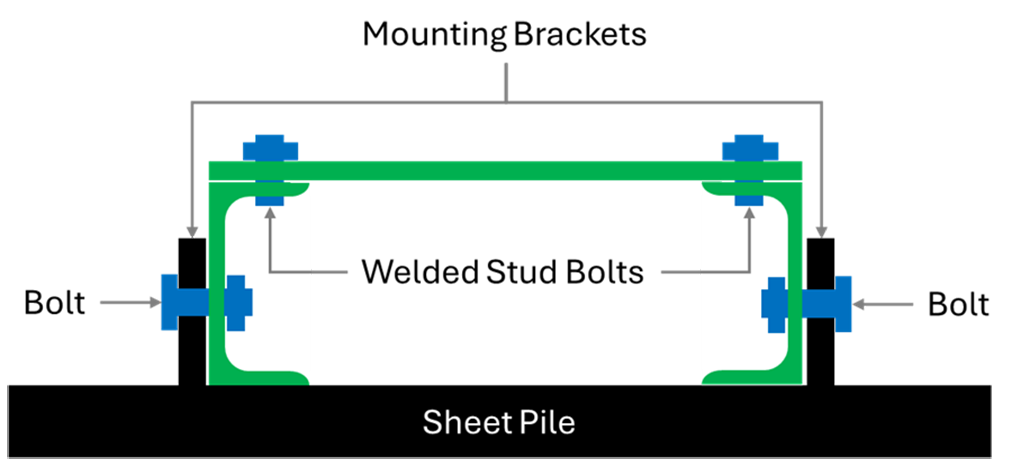
Figure 2. Bonded Sensor Protection Design
Both designs were tested through a pile driving test using a sheet pile. The bonded design performed well, surviving peak pile driving accelerations of up to 900g, while the bolted design failed in the bolted connection near the top of the protection system. Strength and fatigue analyses were conducted with the bolted design to investigate the failure mode.
Figure 3 shows the sheet pile with prototype sub-seabed sensor protection system test article just prior to the pile driving test and a simulation using FEA. During testing, accelerations and strains were specifically monitored at the top of the pile using a PDA-8G Pile Driving Analyzer from Pile Dynamics Inc (PDI). The testing and analysis was focused on the sub-seabed sensor protection systems and their interaction with the pile, particularly at potential weak points. Data collected helped evaluate the load impacts on the sub-seabed sensor protection systems, compare them to expected monopile installation loads, and provide input for the FE analysis. During testing, the topmost bolts failed in the bolted design at a depth of 23.5 ft., just shy of the 25 ft. target. While no bolts failed in the bonded design, many of the bolts were loose after pile extraction.
The FEA, conducted using ANSYS Mechanical, used the measured acceleration data from the pile driving test to establish the range of loads to be simulated. A quasi-static approach was chosen to estimate maximum stresses at the system’s interface with the pile and to identify stress concentration areas where failures might occur. This method assumes that all energy from the pile driving is absorbed by the cable protection system, without transfer to pile movement or soil damping, making it a conservative stress calculation approach.
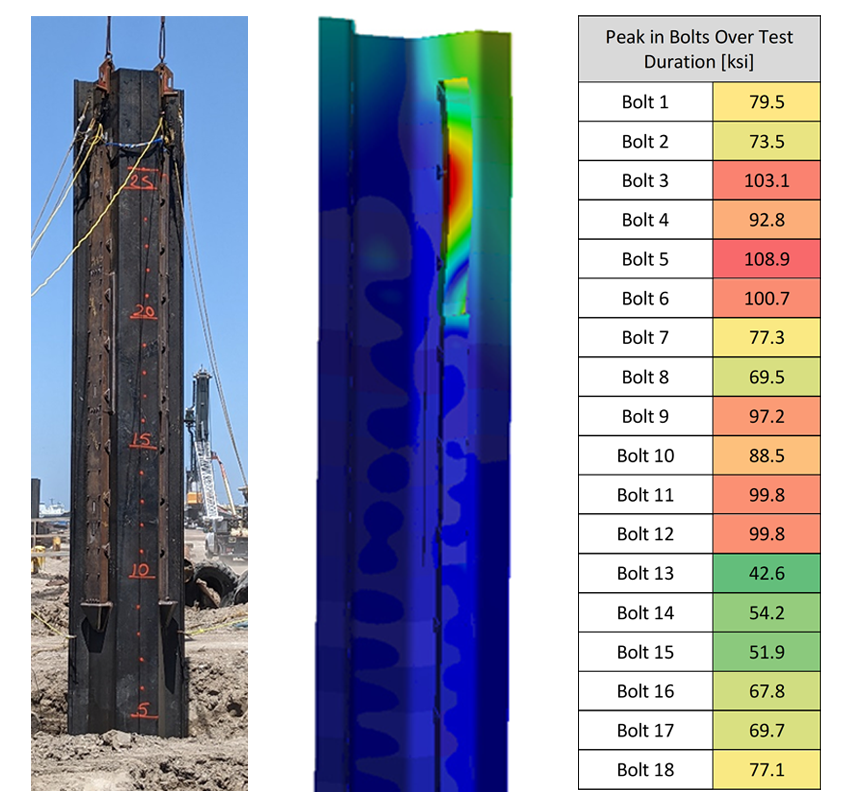
Figure 3. Left: Sheet Pile with Prototype Protection System and Right: Strength Finite Element Analysis Results
Fatigue damage from the pile driving was estimated using DNV RP C203, applying the Palmgren-Miner rule to calculate fatigue damage accumulation. The vibration response of a pile during pile driving is highly dynamic, making evaluation of the cyclic stress history for each hammer blow computationally intensive and sensitive to detailed soil conditions, which are not fully available for the study. As a result, each blow was treated as a single cycle for fatigue calculations, acknowledging that a dynamic analysis for each blow could potentially offer a more precise damage estimate but was not feasible due to high computational demands and insufficient data on soil properties.
The FEA and fatigue analysis results align well with the test observations. The analyses indicated that the bolts near the top of the test articles had the highest stresses and the largest fatigue damage. The analysis results showed that the peak stress in the bolts was very high. Additionally, fatigue analysis showed that the topmost bolts would fail at a depth of around 23 ft, aligning well with testing. As a result, failure via overload, fatigue, or a combination thereof are plausible, but further work is needed to determine which mechanism was the most likely cause.
It can be concluded from testing and supporting FEA that sub-seabed monitoring of monopile foundations can be fabricated from low-cost, off-the-shelf components. While failure occurred during testing, several design modifications were suggested that could mitigate failure of the protection system moving forward. The successful implementation of these sub-seabed sensor protection systems illustrates that effective sub-seabed sensing can be achieved economically with off-the-shelf materials and collaborative design efforts, ultimately reducing operation and maintenance costs for offshore wind farms.
“The successful implementation of these sub-seabed sensor protection systems illustrates that effective sub-seabed sensing can be achieved economically with off-the-shelf materials and collaborative design efforts, ultimately reducing operation and maintenance costs for offshore wind farms.”
Impact:
SES Renewables Solutions’ innovative approach has set a new standard in the industry, offering a scalable and economically viable solution that enhances the structural health monitoring of offshore wind foundations. This initiative not only supports the sustainability goals of the offshore wind sector but also extends the operational lifespan of wind farms, ensuring they continue to contribute to global renewable energy targets effectively.
______________________________________________________________________________________
This article summarizes the research presented in the technical paper “Low-Cost Below Seabed Monitoring Solutions for Monopile Foundations,” a technical paper by William P. Walker and Ryan S. Williams and presented at the 2024 Offshore Technology Conference in Houston, Texas. The paper is catalogued as OTC-35186-MS.
Other Case Studies
Micro/Smart Power Grid Sustainability Initiative Proposal
Rural Panama Micro/Smart Power Grid Sustainability Initiative
View the case studyMicro/Smart Power Grid Sustainability Initiative Proposal
Rural Panama Micro/Smart Power Grid Sustainability Initiative
View the case studySafety Testing of Flow Batteries for Grid Storage Applications
Research studies determined the safety and performance characteristics of flow batteries.
View the case studySafety Testing of Flow Batteries for Grid Storage Applications
Research studies determined the safety and performance characteristics of flow batteries.
View the case studyNeoSight: Asset integrity Management in the Digital Age
An asset integrity management tool that helps to significantly reduce unexpected failures.
View the case studyNeoSight: Asset integrity Management in the Digital Age
An asset integrity management tool that helps to significantly reduce unexpected failures.
View the case study