Energy Storage, Hydrogen, Wind
Stress Engineering Services, Inc. launches SES Renewables Solutions
January 31 2023
Wind
The Future of Offshore Wind is Floating; Are We Ready?
January 30 2023
An Overview of the Technical and Supply Chain Challenges Facing Floating Wind
By William Walker, Ph.D.
“At Stress Engineering Services, we’ve been working in energy for 50 years. Our decades of experience in traditional energy solutions, combined with our unparalleled technical expertise across all other business areas, such as aerospace and defense, consumer products, and medical technologies, are the ideal toolbox to address the technical and commercial challenges renewable energy faces.” -Jack Miller, President, Stress Engineering Services
Introduction
The offshore wind industry is experiencing significant growth globally, with numerous countries setting national goals for development by the end of the decade. Much of this global offshore wind growth is expected to be floating wind. In December 2022, the Bureau of Ocean Energy Management (BOEM) held the United States’ first lease auction on the pacific coast, where the water depth will require floating wind technology. Additionally, BOEM plans to lease auctions in Oregon, the Gulf of Mexico, the Gulf of Maine, and the Central Atlantic within the next few years. Some of these lease areas will require floating technology.
Outside of the United States, there have been significant advances in floating wind development. For example, in February, the United Kingdom’s ScotWind auction included 15 G.W. of floating wind lease areas, and similar strides toward floating wind are happening in other regions of Europe and Asia.
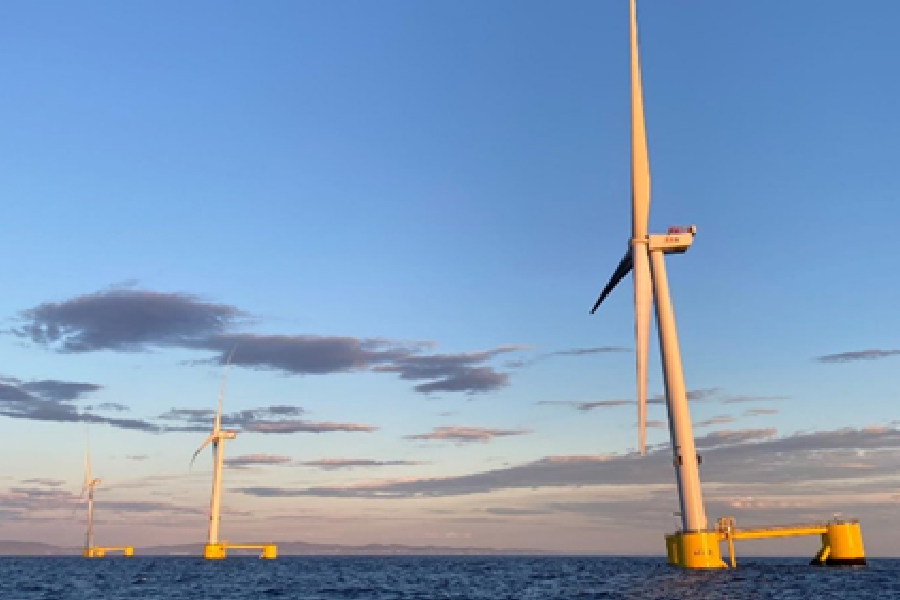
Figure 1. Windfloat Atlantic
Currently, floating offshore wind is still in the pilot project stage, and as of the end of 2021, there were ten floating wind pilot projects in operation between Europe and Asia [1]. However, now that commercial-scale floating wind has entered the pipeline, the technology and infrastructure required to bring these projects to life need to be commercialized. With nearly 80% of the world’s offshore wind resources existing in water depths greater than 60 m (58% of the United States resource), the future of offshore wind undoubtedly includes significant amounts of floating wind farms. In this article, I discuss the industry’s technical and supply chain challenges.
Technical Challenges
Floating wind has been an important industry discussion topic in 2022. Much of the technology floating wind farms will require is under development, and pilot projects are currently in operation. However, the industry is not well established like its fixed-bottom counterpart, and there is still a wide range of research and development needed to make this industry a reality.
As we discuss technical challenges, it is essential to note that we are implying the challenges centered around developing economical, technical solutions. In other words, does the technology that enables an economic Levelized Cost of Energy (LCOE) exist? Current demonstration projects in Europe and Asia provide great insight into this question, as does our 50 years of experience serving the offshore oil & gas industry at Stress Engineering.
At SES Renewables, Stress Engineering’s renewable energy group, our team has a long history of offshore engineering and sees several significant challenges that should be addressed to develop low-cost solutions for floating wind.
Mooring Reliability
Floating wind turbines use the minimal number of mooring lines possible to maintain a station (e.g., 3 or 4 lines). While a solution with three lines keeps the floater in place, it offers little room for failure and no redundancy.
The oil & gas industry typically uses far more mooring lines (e.g., 16, 24 lines). This is partly due to the extensive production facilities requiring additional station-keeping lines. Additionally, it provides redundancy in the event a mooring line fails. Moreover, failed mooring line scenarios are considered in design with the expectation that it could occur.
If a mooring line breaks in a 3-mooring-line scenario, the floater will not be able to maintain the station effectively. Consequences of such a failure may include failure of the other two mooring lines and the power cable. Furthermore, if a floater came completely unmoored, it could impact other turbines in the field, and the asset itself could be lost. The costs incurred by lost production, rebuilding, and reinstalling a floating wind turbine could be pretty significant, as evidenced by such failures in the oil & gas industry [2]
Mooring line failures occur, and the oil & gas industry has seen its fair share. The probability of a failure is highest after installation (i.e., due to an installation error), near the end of its life, and during severe weather events (e.g., hurricane, tsunami). Unfortunately, the current pilot projects haven’t operated long enough to see how these systems will behave in the latter portion of their design lives.
Mooring and Anchoring Costs
Mooring and anchoring are significant expenses in any offshore development, which could be substantial for deep-water floating wind farms. For example, consider a 100-turbine wind farm in a 1000-meter water depth in a 3-line spread-moored configuration. Each mooring line may need to be 2000 meters in length, which would be a total of 600 km of mooring line. Manufacturing, transporting, and installing such a large number of mooring lines and anchors is unprecedented, far beyond anything the offshore oil & gas industry has undertaken. As a result, the cost and the time required will be high.
Shallow Water Mooring
The mooring challenges differ in shallower water floating wind farms (i.e., 60 – 300 meters). The oil & gas industry doesn’t use floaters in such shallow water depths, and the typical spread moored solution oil & gas has utilized for decades may not work well in these water depths. As a result, taut or semi-taut solutions may be needed.
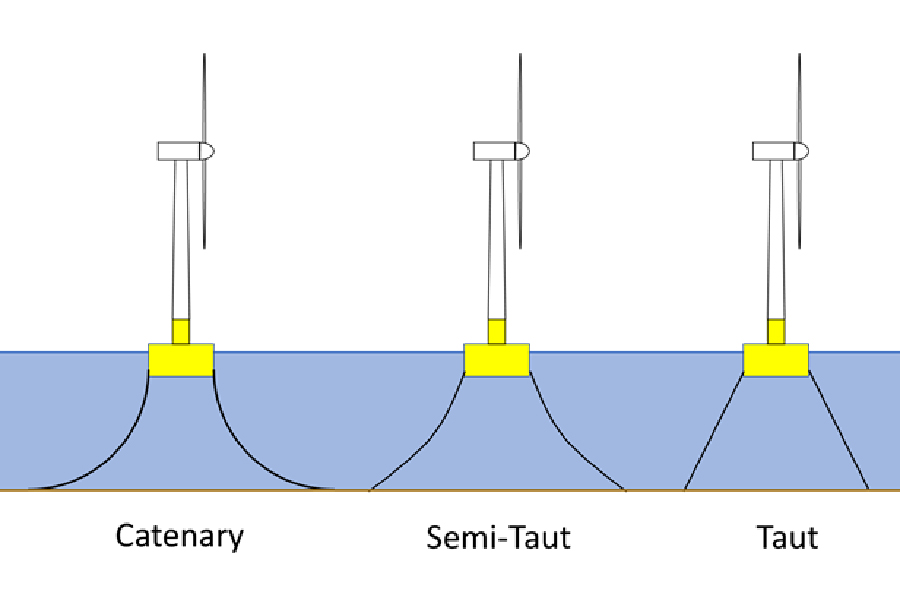
Figure 2. Mooring Systems
Unlike a spread-moored catenary system, taut or semi-taut mooring systems require a method of compliance in the heave direction (i.e., in-line spring). This is also true of a tension-leg platform (TLP) in shallow water. Additionally, the anchors need to accommodate a vertical component of the tension load in the mooring line. As a result, lower-cost drag-embedment anchors may not be feasible, and suction anchors may be needed, which can be expensive.
Operations & Maintenance Costs
Inspecting and maintaining floating systems can be expensive. Floating wind turbines are unmanned, and a physical visit to the facility is required for inspections. Inspection of subsea equipment, including hulls, mooring components, and power lines, is challenging. Blade replacements are expensive and hard to do in intense water. As these facilities age and more details fail, maintenance costs increase even further. Many of the pilot projects consider towing the floater back to port. While this is a feasible solution for pilot projects, it may be too expensive at the commercial scale [3]. Additionally, O&M cost reduction is seen as a significant strategy for reducing LCOE [4]
Supply Chain Challenges
While the upcoming floating wind industry faces numerous technical challenges, these can be solved through sound engineering and technology development. However, the scale of floating wind (e.g., the number of floaters as compared to oil & gas), and regional supply chain pose additional challenges for this industry [3].
Serial Fabrication
The scale of manufacturing the floating wind industry will require is unprecedented. Nearly every facility the oil & gas industry has built has been a single, custom-built system. Design and fabrication methods may also struggle to meet the demand and timeline the floating wind industry will command. Building floaters in today’s offshore oil & gas industry is a month-long process and building tens or hundreds of these in a short timeframe may seem impossible. Manufacturing at the scale commercial floating wind will require is going to be a significant challenge and may require an evolutionary change to the manufacturing approach akin to Henry Ford and the assembly line.
“Mr. Edison gave America just what was needed at the moment in history. They say that when people think of me, they think of my assembly line. Mr. Edison, you built an assembly line which brought together the genius of invention, science, and industry.” -Henry Ford
This challenge applies to components other than the floater itself. The number of anchors and mooring lines needed to install tens of hundreds of floaters is beyond anything the oil & gas industry has done before and may impose challenges in meeting demand and timeline.
Infrastructure
Similar to the fabrication challenges, the floating wind industry is forming in many regions with little or no existing infrastructure to support offshore operations. For example, California does not have the infrastructure or the appropriately skilled workforce to support this industry. Domestic and local content requirements may exacerbate this challenge.
Other Challenges
Most of this article has been focused on the technical and engineering challenges surrounding the development of floating wind, but there are other challenges worth noting which include:
- Environmental impact of seabed catenary mooring chain interaction.
- Coexistence with other ocean users. Mooring takes up a lot of space and floating wind could significantly impact other ocean industries, such as fishing.
How We Can Get There
In order to reach current floating wind targets at an economical LCOE, tremendous effort needs to go toward addressing the challenges described herein. While challenging, they are not insurmountable, and, as a company with decades of offshore engineering experience, we at SES Renewables recommend the following actions for the industry:
- Develop cheap O&M solutions. Operation and Maintenance costs can be significantly reduced through condition-based maintenance (CBM) programs that utilize condition monitoring and physics-based digital twins. Offshore wind typically considers less conservatism in design than oil & gas, yet oil & gas still see’s failures. An effective CBM program could help prevent unexpected failures (e.g., mooring line failure). Additional benefits of CBM could design life extension.
- Study shallow water mooring concepts, particularly those using polyester rope and nylon rope mooring. Research needs to be directed toward understanding the behavior of these materials, particularly regarding load elongation, creep, and fatigue.
- Consider new anchor concepts that use different materials. For example, the use of materials such as concrete may provide a lower-cost, domestically available solution for anchors.
- Design for serial manufacturing and quick installation. The oil & gas industry has great solutions for floating systems; however, these solutions were not developed with the primary goal of quickly manufacturing and installing them. The floating wind industry should optimize component designs so that they can be fabricated and installed cheaper and faster.
- Invest in the supply chain in the U.S. and potentially Mexico. The supply chain and infrastructure challenges floating wind faces in California are significant. The U.S.-based oil & gas supply chain can help support the demand; however, Mexico also has a strong oil & gas supply chain and offers another source of supply that could be considered.
- Utilize oil & gas expertise. The oil & gas industry has decades of experience in solving technical problems for floating systems which can provide valuable support for the floating wind industry.
- Advanced research and development through Joint Industry Projects (JIPs). JIPs are a great way for the industry to collectively advance research and solve challenges that are common across the industry. Many of the challenges discussed in this article are perfect JIP topics.
References
[1] Offshore Wind Market Report: 2022 Edition, U.S. Department of Energy, Office of Energy Efficiency and Renewable Energy, 2022.
[2] A Historical Review on Integrity Issues of Permanent Mooring Systems, Kai-tung Ma; Hongbo Shu; Philip Smedley; Didier L’Hostis; Arun Duggal, OTC-24025-MS, Offshore Technology Conference, Houston, Texas, USA, May 2013.
[3] Floating offshore wind challenged by supply chain conundrum, https://splash247.com/floating-offshore-wind-challenged-by-supply-chain-conundrum/.
[4] 2020 Cost of Wind Energy Review, T. Stehly, P. Duffy, National Renewable Energy Laboratory, Golden, CO, NREL/TP-5000-81209.
[5] Windfloat Atlantic, https://www.windfloat-atlantic.com/.
Hydrogen, Wind
Offshore Wind Hydrogen Production
June 20 2022
An Overview of the Technical and Regulatory Challenges
William Walker, Ph.D.
Colton Sheets, PE
Introduction
The United States has set a goal of developing 30 GW of offshore wind by the end of the decade. To achieve this, the Bureau of Ocean Energy Management’s (BOEM) will be leasing regions in all coastal regions of the United States including the Atlantic coastline, Pacific coastline, and Gulf of Mexico. While most offshore wind developments will be dedicated to grid electricity production, there is increasing interest in hydrogen production through electrolysis, particularly in the Gulf of Mexico which has existing infrastructure to support the industry.
Offshore wind hydrogen production facilities must produce hydrogen in a cost-effect manner while also considering safety, protection of the environment, prevention of waste, and conservation of natural resources. The experience gained from oil and gas development will provide the industry with a solid foundation, but new capabilities, approaches, and processes will be required to ensure the safe installation and operation of the latest energy resources. This white paper introduces many of the considerations needed for safe and cost-effective hydrogen production from offshore wind.
Producing Hydrogen Offshore
Significant advances in wind energy technology has led to wind turbines of increasing capacity in search of consistent wind resources. This has resulted in a significant increase in offshore wind farms globally and led to numerous developers pursuing wind farm development on the United States. At the same time, the role of electricity generated by wind turbines is being revisited, from a direct input into the US electrical grid, to the mechanism for hydrogen generation through electrolysis. The offshore environment is ideal for this method of hydrogen production considering the abundance of water. Figure 1 is a schematic showing an overview of producing green hydrogen via offshore wind and electrolysis. The term ‘green’ hydrogen simply means hydrogen produced using clean energy.
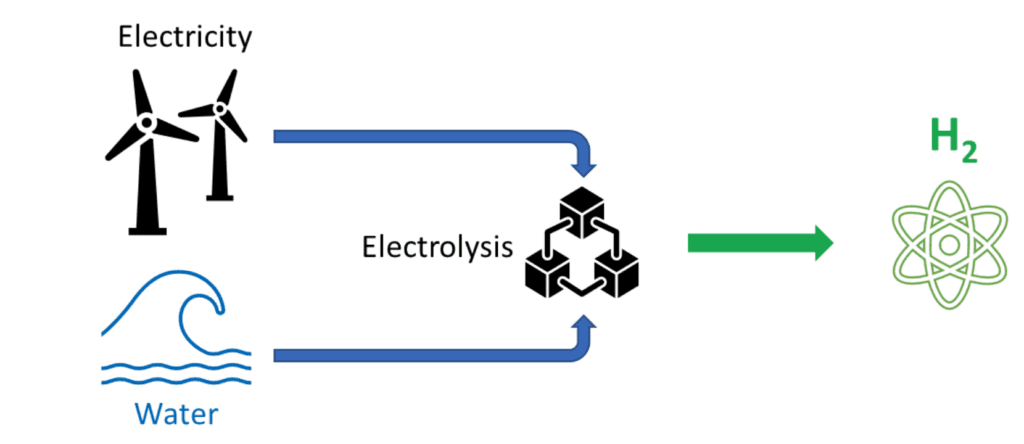
Green Hydrogen Production
The basic concept behind green hydrogen production involves using electricity generated by renewable energy sources (e.g., offshore wind turbines) to separate hydrogen from water via electrolysis. Hydrogen is a desirable output of this process as it is a clean burning fuel and can be stored for long periods of time. There are multiple methods operators could choose to execute this process, many of which are already being considered at a conceptual level.
Hydrogen Specifics
Before the methodologies for hydrogen generate/production, storage, and transmission are discussed, it is important to provide background on characteristics of hydrogen that make it uniquely challenging. Natural gas will be used for comparison purposes as it is a gas well understood in offshore production, handling, and storage. Table 1 below lists several parameters and their associated values for hydrogen and methane (the primary component of natural gas).
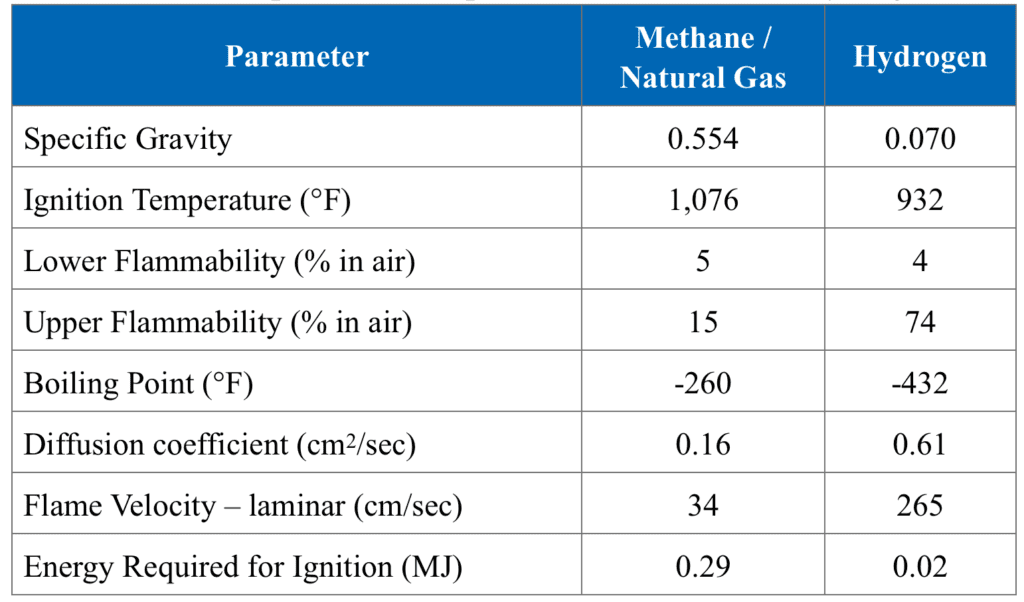
Comparison of Properties for Methane and Hydrogen
The information contained in Table 1 highlights many reasons why hydrogen presents unique challenges to handling and storage. Like natural gas, it is colorless, odorless, tasteless, and non-toxic. Detection of hydrogen is challenging as it is highly diffusive, and odorants are not easily added. Because of its small size and weight, it produces higher leakage rates than many common gases and can permeate through both metal and non-metallic materials. Hydrogen is also extremely flammable and creates a very high explosion risk when allowed to mix with air. The lower flammability limit of 4% means that a hydrogen leak in a confined space could quickly reach a flammable condition. As shown in Table 1, the energy required for ignition is about 1/10th of that required for natural gas. In addition to this, a hydrogen flame is nearly invisible in daylight and produces little radiant heat. This means that a hydrogen flame would not be sensed until it is extremely close.
In addition to safety challenges presented by hydrogen, it is also known to have detrimental effects on the materials used in transportation and storage due to the potential for embrittlement under certain conditions. This phenomenon can lower material toughness, which in turn reduces critical flaw size and potentially increases required inspection intervals.
Conceptual Approaches to Production, Storage, and Transportation
Conceptually, there are many potential configurations for production, storage, and transportation of hydrogen produced using offshore wind. Figure 2 of the U.S. Dept. of Energy Hydrogen Program Plan (https://www.hydrogen.energy.gov/pdfs/hydrogen-program-plan-2020.pdf) provides a good summary of the various technology options that may be considered. This section focuses specifically on hydrogen produced with offshore wind. One example involves producing electricity using offshore wind and sending it onshore for electrolysis. This process could be completely isolated from the electrical grid or only some of the electricity could be used for onshore hydrogen production. This method would not require any additional requirements beyond those for offshore wind farm development. Other methods involve performing electrolysis offshore and transporting the hydrogen back to shore. Right of way and installation requirements will vary depending on the methodologies used. The conceptual examples outlined below are intended to demonstrate the variety of possibilities associated with offshore hydrogen production using offshore wind and the breadth of knowledge that would be needed for an overseeing regulatory body.
Concepts that may be considered for producing hydrogen include:
- Generating hydrogen from seawater with fixed offshore wind turbines. The electrolyzer(s) may consist of fixed offshore structures that could be installed topside on a jacket or subsea.
- Generating hydrogen from seawater with floating offshore wind turbines using several central electrolyzers.
- Generating hydrogen from seawater with floating offshore wind turbines using one electrolyzer per turbine.
Concepts that may be considered for storing hydrogen include:
- Storing hydrogen on a Floating Production, Storage and Offloading unit (FPSO). This concept may consist of cryogenic transport of hydrogen similar to techniques used for LNG.
- Storing hydrogen in subsea storage units. This could involve an array of subsea pressure vessels.
- Storage in depleted oil/gas reservoirs
- Storing hydrogen on each floating offshore wind turbine unit.
- Converting hydrogen into ammonia for safer storage and transportation.
Concepts that may be considered for transporting hydrogen include:
- Cryogenic tankers similar to LNG equipment
- Pipeline systems. Either new construction or using existing systems.
- Injection into existing natural gas lines for hydrogen-natural gas blending
Challenges Introduced due to Conceptual Approaches
The previous section outlined some of the numerous concepts that operators may consider for green hydrogen production offshore. These concepts introduce new challenges that should be taken into consideration. A few examples are provided below.
Some new considerations introduced by producing hydrogen with offshore wind include:
- Challenges implementing and operating electrolyzers in an offshore environment topside or subsea.
- Power transmission to the electrolyzer, especially subsea.
- New infrastructure required for gathering produced hydrogen and sending to transportation and storage systems.
Some new considerations introduced by storing hydrogen offshore include:
- Accounting for, detecting and handling potential hydrogen leaks. For example, consideration should be given to leakage in confined areas.
- Infrastructure for storing hydrogen in liquid form (i.e., storage units, compressors, transport systems) will need to be designed to withstand the required pressures and cryogenic temperatures (-430 °F).
Some new considerations introduced by transporting hydrogen offshore include:
- Traditional offshore risers and pipelines often utilize high-strength steels. Hydrogen embrittlement should be considered in design.
- Environmental concerns associated with hydrogen’s increased potential for leakage and flammability. In the event of a hydrogen leak in the ocean, consider the impact to both the transportation infrastructure and the ocean environment.
The items above account for only a small portion of the questions operators and regulators of offshore hydrogen generation should consider. Importantly, other technological advances have provided example frameworks for filling knowledge gaps through empirical and analytical research and industry collaboration. The use of joint industry projects and dedicated research efforts should be used to advance collective knowledge of the regulatory body.
Moving the Industry Forward
With 50 years of experience in energy, SES Renewables is an ideal party to perform research and conduct JIPs that identify and address the knowledge gaps in the green hydrogen industry. The topics listed below are examples of potential gaps that could be addressed.
- Establishing the effect of produced hydrogen on metallic and non-metallic material performance, specifically fracture toughness values for materials used during production, transportation, and storage. For non-metallic materials, quantifying hydrogen permeation rates, possible sealing issues, and potential susceptibility to rapid gas decompression.
- Determination of process safety requirements for offshore operations related to hydrogen production including leak detection, fire prevention, and blast zones in the event of detonation.
- Assessing the environmental effects of a significant hydrogen leak from transportation pipelines or storage facilities. Understanding the potential impacts to personnel, marine life, and plant life in the vicinity of the leak.
- Identification of acceptable inspection techniques and technologies and suitable repair methodologies for remediation of identified damage and defects.
- Development of a guidance document focusing on a state-of-the-art assessment of hydrogen production and handling. The document would identify industry best practices and the latest technologies. Additionally, this document could provide a roadmap and standardized process for future regulators assessing new offshore hydrogen developments and associated technologies.
- Development of a response plan that should be undertaken by operators in the event for leaks or unexpected catastrophic failure.
Closing the knowledge gaps will require collaboration between industry stakeholders, regulators, and other public and private entities. This white paper provides a general overview of the requirements needed, as well as targeted initiatives that should be undertaken as we embark on this next wave of offshore energy development. Contact SES Renewables to discuss your green hydrogen project or technology.